Our Products
Valves
Industrial valves are of various types such as Gate Valves, Globe Valves, Ball Valves, Butterfly Valves, Check Valves, Pressure Valves, and Diaphragm Valves etc. These valves perform various functions working on a different working principle.
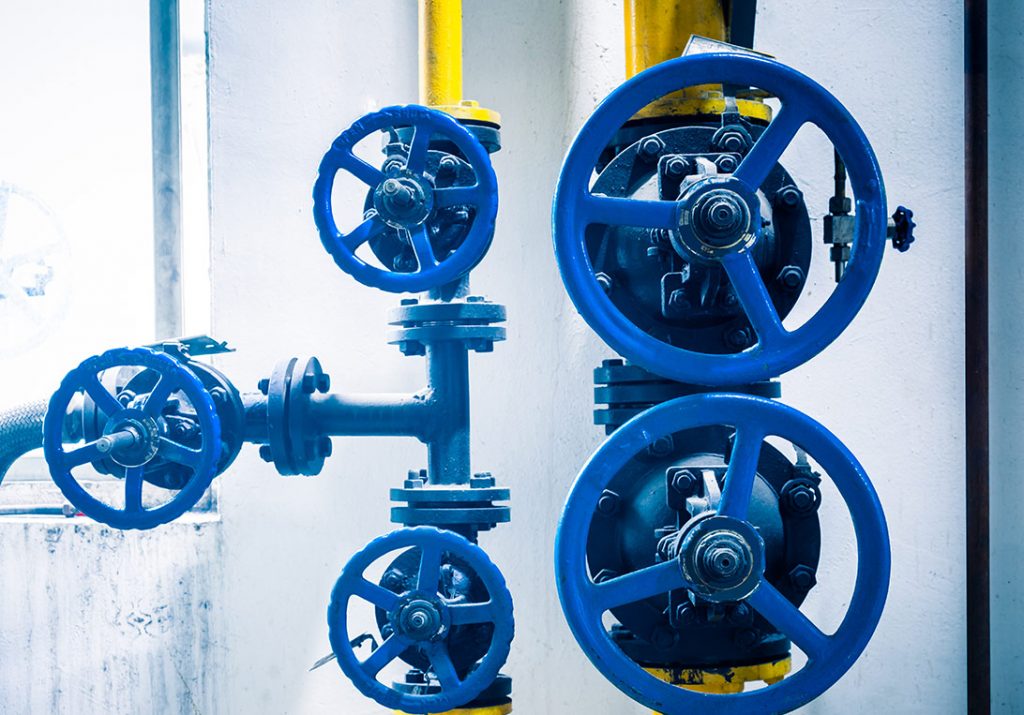
Ball Valves, used for flow control and whenever tight shut-off is required, have accounted for over 19% of the revenue share in 2014.
In the recent years, there is a huge demand for butterfly valves as they are used extensively in the automation, oil & gas industries.
Check valves’ are going to witness a sturdy growth, with a CAGR of over 7% in the next coming years. These unidirectional valves are used to evade the process flow from returning to the system, thereby preventing it from damaging the equipment and disrupting the process.
Gate, Globe, Check, Ball, Strainer, Plug. | |
SIZES | 1/2" - 64" |
PRESSURE | 150#, 300#, 600#, 900#, 1500# |
BODY | Cast Steel & Forged Steel |
MATERIAL | SS, CS, Alloy |
ENDS | Flanged, BW, Threaded & SW |
Types of Industrial Valves
Industrial valves are devices that are used to regulate liquids, gases, and slurries. The flow of liquids or gases can be controlled using these valves. This can be done through pipes and other passageways by opening, closing, and partially obstructing the passageway or pipe.
Different types of Industrial Valves include:
- Gate Valves
- Globe Valves
- Ball Valves
- Butterfly Valves
- Check Valves
Types of Industrial Valves
Industrial valves are devices that are used to regulate liquids, gases, and slurries. The flow of liquids or gases can be controlled using these valves. This can be done through pipes and other passageways by opening, closing, and partially obstructing the passageway or pipe.
Different types of Industrial Valves include:
- Gate Valves
- Globe Valves
- Ball Valves
- Butterfly Valves
- Check Valves
Gate Valves
Gate Valves are designed to serve as isolation valves. These valves help to control the flow of liquid through the pipes. To start or stop the water flow or any other kind of liquid, these valves are affixed to the pipelines. Gate valves are used for various purposes and they can be seen commonly in homes and commercial centers. Different materials such as stainless steel, cast iron, alloy steel, forged steel etc are used to manufacture these valves.
Gate valves are used to either halt or start the flow of water. Functioning of gate valves includes the lifting of a circular of the rectangular gate out of the fluid path. When gate valves are open, there will be nothing to obstruct the flow as the pipeline diameter and gate have the same opening. The valve size can be determined with this bore diameter.
Advantages
- Gate valves contain very low friction loss
- They can be used both ways in the circuit
- They provide laminar flow, a pressure loss is minimum
- Gate valves help to save energy and reduce total cost of ownership
- There will be low-pressure drop when opened fully and tight sealing
Disadvantages
- Gate valves cannot be opened & closed quickly
- They cause vibrations
- In systems where high-temperature changes irregularly, due to the load in pipe at the valve end, leakages in gate valves occur.
- The operation, maintenance, and repair of gate valves seating surfaces are complex.
Applications:
- Gate valves are suitable to use in high temperature and pressure conditions.
- They are used for on-off applications
Globe Valves
Globe Valves are among the most popular type of valves used in various applications. These valves are similar to gate valves and use linear motion to throttle flow. They are used to control the flow in a pipeline and they regulate by the position of a movable disk (or plug) in relation to the stationary ring seat. The major advantage of a globe valve is, it does not leak as much as other valves.
Globe valves are composed of a baffle that splits the inside of the pipe, which is typically parallel to the pipe's length. They are named for their spherical body shape with the two halves of the body being separated by an internal baffle. It consists of a movable disk-type element and a stationary ring seat in a generally spherical body.
Advantages
- Globe valves throttling, the full-closing characteristic is good.
- The opening-closing time is shorter.
- Body ring seating surface process is easier.
- They can be used as stop-check valves.
- They contain positive shut-off
Disadvantages
- Pressure loss is higher
- To close under high pressure, globe valves require a larger amount of force or an actuator with a large torque.
Applications:
Global valves are used primarily for throttling purposes. They may be considered as general purpose flow control valves that are used for high-temperature applications.
Ball Valves
As the name suggests, ball valves are valves that use a ball to control the flow of material from one orifice to another. These valves work by allowing the orifice to be open, blocked, or partially opened to regulate gas/liquid flow. Ball valves are an ideal choice for use with gases as they can provide a better seal. They are very versatile as they withstand pressures of up to 700 bar and temperatures of up to 200 degrees Celsius, and their sizes typically range from 0.5 cm to 30 cm. They are easy to operate and repair because they have a simple structure.
They are designed with special measures that allow only the 90 degree rotation required to open and close the ball valves. These valves are a notable industrial choice due to their reliable and air-tight sealing in the closed position.
Advantages
- They have a compact and low maintenance design that does not require lubrication
- They are the most affordable of all faucets
- The biggest advantage of ball valves is that they have poor throttle characteristics which can cause the seat of the ball valve to erode easily.
- They provide anti-leakage services.
- They open and close quickly.
- Ball valves have multi-way design flexibility.
Disadvantages
- Ball valves are not suitable for permanent throttle.
- In the remaining fluids, the particles in the fluid collide with the surfaces and stick to them. This may cause leakage, abrasion and other problems.
Programs:
- Ball valves are used to control flow and pressure and shut off for corrosive fluids, slurries, liquids and common gases.
- They are used in the oil and natural gas industry as well as chemical storage
Butterfly Valves
Butterfly Valves are designed to regulate flow, but with limited control capability. Butterfly valves are easily operated by rotating a handle 90 degrees. It consists of a metal disc in the body of the valve which is positioned perpendicular to the flow in the closed position. Regulation of liquid flow can be allowed through intermediate rotations. Butterfly valves are configured to operate electronically, manually or pneumatically.
They can be used for a broad range of applications within water supply, wastewater treatment, fire protection and gas supply, in the chemical and oil industries, in fuel handling systems, power generation etc. These valves can be operated by handles, gears or actuators according to specific needs.
Advantages
- Butterfly valves are very accurate, which makes them advantageous in industrial applications.
- They are quite reliable and require very little maintenance.
- They have the capability to throttle flow.
- They can be installed or removed without pipe system dislocation
Disadvantages
- Butterfly valves have no tight shut offs
- Some portion of the disc is always presented to the flow, even when fully opened. This may result in a pressure switch across the valve, regardless of the setting.
Applications:
- Butterfly valves can be used in pharmaceutical, chemical, and food processing services.
- They are used for corrosive liquids at low temp and pressure.
Check Valves
Check Valves are also known as Non Return Valve (NRV). They allow liquid to flow in one direction only and prevents back flow of media in the reverse direction. The purpose of check valves is to prevent process flow from reversing in the system which could damage equipment or upset the process.
They are commonly found protecting pumps in liquid applications or compressors in gas systems where backflow could cause the pump or compressor to shut down. The basic design of a check valve reduces backflow in a line.
As they have a simpler design, they can operate without human interaction and automation. They rely on the flow velocity of the fluid to open and close. The higher the flow rate, the more open the valve will be until it reaches it maximum, full open position.
Advantages
- Check valves prevent backflow
- They can sustain pressure
- Check valves serve as backup system
Disadvantages
- They cannot be used with pulsating systems
- Closing element may crash causing damage and excessive wear
Applications:
- Check valves are used in a variety of markets and applications as they contain simple design and versatile material options.
- They help to prevent backflow and maintain pressure.
- Check valves can be seen in industries such as refining, petrochemical, chemical, etc., oilfield production, water, steam, refining petro, and viscous fluids.
- They are also commonly found in waste-water management systems and in manufacturing.
Industrial Valves can be bought at affordable price rates from the global manufacturers.